- ABOUT DIAPHRAGM TYPE COMPRESSORS
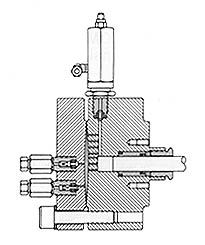
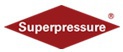
FEATURES
|
|
HOW IT WORKS
The
Compression ratios up to 14 to 1 are obtained for each stage. The unique design provides for an absolute minimum of dead space. In operation, the plunger of the compression head is reciprocated as in a pump. Oil from the storage bulb is compressed by the plunger, which in turn pulses the diaphragm. The fluid to be compressed is taken in and discharged on the opposite side of the diaphragm through the check valves in the head plate on the down and up stroke of the diaphragm. Oil is drawn into the chamber beneath the diaphragm by the suction created on the plunger backstroke. Excess oil in the chamber can flow back to the storage bulb during the forward plunger stroke through the pressure limiting device. This built-in hydraulic device is manually adjustable and ensures that the discharge pressure of the compressor cannot exceed a preset limit. The plunger stroke is preset so that under normal operating conditions, oil will not flow through the pressure limiting device unless the maximum discharge pressure is exceeded.
These compressors may be easily cleaned in accordance with the most stringent specifications. Fluids other than ordinary oil, such as oxygen-compatible flourinated products, may be used for diaphragm pulsing if required for specific applications. Compressors can be constructed of materials other than those normally supplied for particular corrosion-resistant applications on special order.
These compressors are adaptable to either gas or intermittent liquid service. Change-over from one to another is accomplished by interchanging a set of inlet and discharge check valves. Typically, gas check valves are standard with the compressor; liquid check valves can be specifically ordered. In operating these compressors, particular care should be taken to keep the fluid being compressed free from solid particulate matter since its presence materially reduces diaphragm life. |
